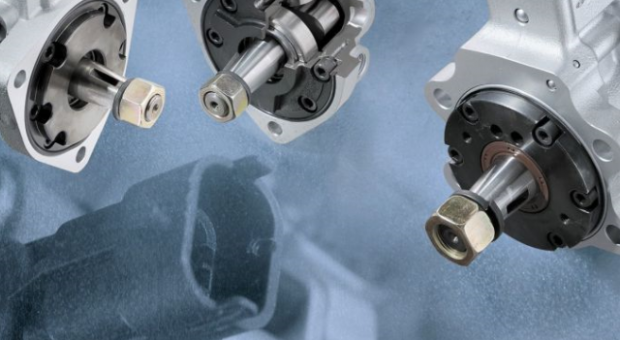
What is a Car Common Rail and Why Its Quality is Highly Important?
The common rail is the most essential component of the direct fuel injection system. Its role consists in accumulating highly pressurized fuel and distributing it to the injectors. The next-generation diesel and gasoline engines tend to become smaller and lighter for less fuel consumption and better performance, which increases the fuel pressure.
This makes out of the common rail a component with very specific requirements. It should possess best mechanical properties in order to be strong and resistant to fatigue, loading, vibration and other environmental conditions. Eventual common rail failure is always critical since the entire vehicle can be blocked or even set on fire.
Exposed continuously to increased pressure and heat, its performance is crucial for the whole system. Most common rail problems are related to the complex geometry of the components and possible cracks caused by material fatigue or during the manufacturing process. Therefore a special attention should be paid to the following: defining and keeping best parameters in the design phase, selecting high-quality resistant steels and excellent expertise in the forging manufacturing process. Following these guidelines guarantees perfection and reliable performance of the entire fuel direct injection. Special attention should be paid to:
1. Design
The early stage of common rail’s development is essential for the later performance of that component. The right geometry and precise parameters prevent a lot of problems that occur later as defects in heading process or material fatigue. For example, modern gasoline engines are smaller and lighter which increases fuel internal pressure and requires common rails with complex shape. Hot forging offers a vast variety of shapes and sizes that can be achieved with high-quality equipment as forging hammers, mechanical presses, screw presses and other tools. Defining end-of-forging temperature, cooling and trimming parameters are also highly significant for most precise geometry.
2. Best Material Selection
The common rail itself acts as a common fuel storing rail and it is permanently exposed to heat and pressure. Therefore, if the raw materials haven’t been selected wisely, quality problems can occur. The most common rail problems related to material selection are shorter product life and reduced fuel accumulation volume.
3. Strength
When forged, the common rail is made of stainless steel and consists only of one piece which eliminates the risk for cracks and leakages. Additionally, forging strengthens the material by closing empty spaces within the metal while deforming and shaping it with localized compressive forces. Every single production step of the common rail manufacturing process should undergo strict control.
The manufacturing company should provide best design expertise, develop most resistant materials, use 100% controlled tools and apply best forging techniques