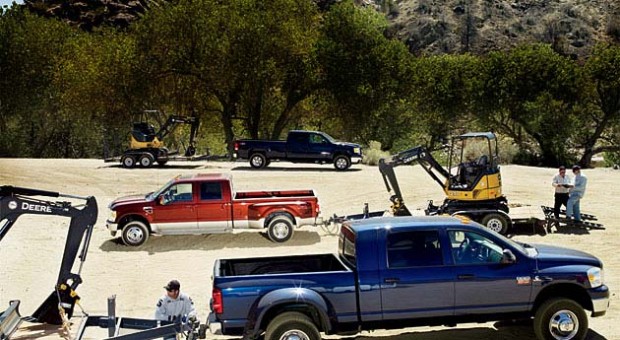
How to make the most of a reefer trailer?
Even the most experienced of shippers have absolutely no clue on the endless possibilities of increasing the profit margin by using a reefer trailer.
Yes, you have read it right. Adding additional reefers to your fleet is a sure shot way to expand your clientele since temperature sensitive freight just cannot be hauled in a regular dry van trailer and what’s more, reefer trailers can also be used to haul dry freight.
The trailer’s insulation value along with its age may affect its running capacity. Continuous running calls for significant fuel consumption and higher operating costs. Temperature variations of 5 or 10 degrees will not affect the quality of most of the products. Some freights may not require steady temperature but the customer may demand continuous running of the trailer despite the need for it.
In such situations acceptable range of temperature should be decided before signing the contract. This would allow the driver to set the required temperature and can still save on operating expense. Large carriers have a knowledge bank of the temperature requirements of the products and are in a better position to enter into rate negotiations. Smaller carriers may seek the help of reefer suppliers to broaden their knowledge horizon.
Now let us get into the things that need to be given a thought before purchasing a reefer trailer.
Before you decide to buy one, it is very important to do some research about the seller and the specs of the reefer that is being offered. If you are thinking of buying a used reefer trailer then make sure to get the cooling system checked by a licensed refrigeration mechanic before you buy.
The newer model reefers are less noisy and are equipped with efficient motors that burn less fuel. Apart from that, these reefers are equipped with alarm systems to alert the driver of any changes in the temperature of the trailer.
However, one needs to consider these factors while ordering a new refrigerated truck.
1. Purchase should be done based on the interior dimensions and without compromising the insulation – The insulation wall should never be reduced in size to accommodate the cargo as there may not be sufficient insulation required to meet the temperature specifications of the product.
2. Choose hinged doors over roll-up doors – Roll-up doors, without doubt is easier to use but it does come with a downside of losing insulation over the course of time. This can eventually lead to temperature problems and higher maintenance costs. Hinged doors helps in maintaining insulation but may not work well with tuckaway liftgate spec.
3. Trucks with power interrupt switches–The blower allows the conditioned air to escape and absorbs warm air each time the rear door opens. This can affect the performance of the refrigeration unit. A power interrupt switch shuts the blower and hence does not allow cool air to escape, and also prevents humid air from entering.
4. Measure the truck’s overall dimension before ordering the chassis – The body vendor may find it impossible to install the chassis if it is larger the truck’s overall dimension. The ones in the liftgate range may encounter loading and unloading issues as it cannot be lowered to the ground if the chassis is very high.
5. Choosing the right floor spec to ensure airflow – Inadequate airflow in the box can cause uneven cooling thereby damaging the freight. Proper airflow will ensure uniform cooling and the floor type plays a pivotal role in this. The loading type necessary for the cargo can dictate the floor type that is required.
6. Do not invest in a less-insulated box to save up- front costs – Going for a smaller refrigeration unit can be quite tempting to the wallet but in all likelihood you would end up paying significantly higher operating costs.
Tips and tricks to maintain the reefer
Insulated cavities should be kept out of water- Repairs to the exterior and interior parts of the reefer needs to be dealt with at the earliest to avoid risking moisture from damaging the insulation. Washing with high pressure cleaners should be done with utmost care.
Never leave the door open while the unit is running – This can risk the door switches being cut off the unit besides the wastage of energy. Some clients may demand the reefers to be run while the trailers are at the docks. In such scenarios it is diligent to keep the engine running at a lower rpm since it can considerably reduce fuel consumption.
Do not wait to get the tears in the trailer skin repaired – Any damage to the trailer skin should be fixed at the earliest. Tears in the skin can cause cool air to escape and the insulation may stand a chance of getting contaminated due to moisture. This can affect the efficiency of the cooling system. Fixing this kind of issue at the earliest can save significant repair costs.
Use the maximum insulation value – Insulation value is measured in UA numbers. A trailer with a higher UA number will only use half of the fuel in comparison to a trailer with a lower UA number.
Adequate training should be imparted to drivers – Drivers should be trained on the technical know-hows of the reefers to prevent mishandling. Training should be given on the uses of these sophisticated controls and how to operate them.
Check for oil leakages – Oil leakages should be regularly checked at the engine as well as the compressor. Hoses and belts also need a regular inspection. Regular units call for an oil and filter change when the milestone of 1500 hours is reached or about once in a couple of months depending on how frequent the truck runs.
Choose extended maintenance packages–This can prolong the oil drain interval by 2-3 times for 3000 – 4000 hours. Regular maintenance is required before each load. All air flow passages should be clean as debris can hinder airflow resulting in uneven cooling. The evaporator should be checked for any accumulation of substances that can potentially affect the cooling.